The Key to Advanced Electronics

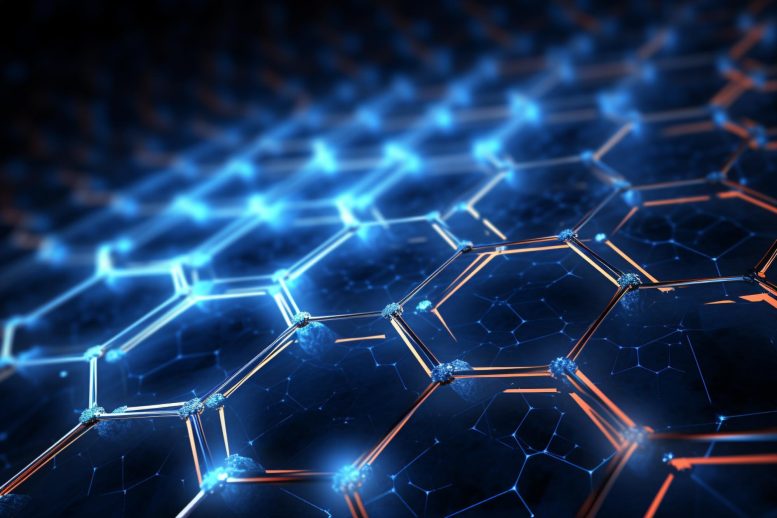
A new method using rotaxane structures to cross-link graphene layers enhances the flexibility, strength, and conductivity of graphene films, with potential applications in advanced electronics and mechanical tools. Credit: SciTechDaily.com
Graphene nanolayers are cross-linked with rotaxanes.
Graphene, composed of layers of carbon atoms arranged in a honeycomb pattern, is recognized as a supermaterial due to its exceptional conductivity and mechanical advantages. These properties are key to advancing flexible electronics, innovative batteries, and composite materials for aerospace applications. Despite these benefits, creating elastic and durable films has been difficult. In a recent edition of Angewandte Chemie, researchers have proposed a solution by connecting graphene nanolayers through extendable bridging structures, potentially overcoming previous limitations.
The special capabilities of microscopic graphene nanolayers often drop off when the layers are assembled into foils, because they are only held together by relatively weak interactions—primarily hydrogen bonds. Approaches that attempt to improve the mechanical properties of graphene foils by introducing stronger interactions have only been partially successful, leaving particular room for improvement in the stretchability and toughness of the materials.
Innovative Cross-linking Technique
A team led by Xuzhou Yan at Shanghai Jiao Tong University (China) took a new approach: they cross-linked graphene nanolayers with mechanically interlocked molecules whose building blocks are not chemically linked, but rather inseparably spatially entangled. The researchers chose to use rotaxanes as their links. A rotaxane is a “wheel” (a large ring-shaped molecule) that is “threaded” onto an “axle” (a molecular chain). Bulky groups cap the axles to prevent the wheels from coming unthreaded. The team built their axle with a charged group (ammonium) that holds the wheel in a specific position.
A molecular “anchor” (OH group) was attached to both the axle and wheel by a linker. The graphene was oxidized to make graphene oxide, which forms a variety of oxygen-containing groups on both sides of the graphene layer. These include carboxyl groups, which can bind to the OH groups (esterification). This reaction allows the wheel and axle to cross-link the layers, after which the graphene oxide is reduced back to graphene.
When these films are stretched or bent, the attractive forces between the wheel and the ammonium group on the axle must be overcome, which increases the tensile strength. Increased stress eventually causes the axle to be pulled through the wheel until it “strikes” the end cap. This motion lengthens the rotaxane-bridges, allowing the layers to slide across each other, which significantly increases the stretchability of the film.
Flexible electrodes made from this graphene-rotaxane foil could be stretched up to 20 % or bent repeatedly without being damaged. They also retained their high electric conductivity. Only stretching by over 23 % led to fracture. The new foils were considerable stronger than foils without rotaxanes (247.3 vs 74.8 MPa), as well as more elastic (23.6 vs 10.2 %), and tougher (23.9 vs 4.0 MJ/m3). The team also built a simple “grasping tool” with mechanical joints that were equipped with and actuated by the new foils.
Reference: “A Stretchable and Tough Graphene Film Enabled by Mechanical Bond” by Chunyu Wang, Boyue Gao, Fuyi Fang, Wenhao Qi, Ge Yan, Jun Zhao, Wenbin Wang, Ruixue Bai, Zhaoming Zhang, Zhitao Zhang, Wenming Zhang and Xuzhou Yan, 03 May 2024, Angewandte Chemie International Edition.
DOI: 10.1002/anie.202404481
The study was funded by the National Natural Science Foundation of China, the Natural Science Foundation of Shanghai, the Shuguang Program of Shanghai Education Development Foundation and Shanghai Municipal Education Commission, and the Starry Night Science Fund of Zhejiang University Shanghai Institute for Advanced Study.